I had rigged up a 24vdc gearmotor to run a drum/spool with cable and was planning to use it to open/close the drop down sides on the high tunnel. The cable would start mounted to the drop down frame, go up and wrap around the drum 4-5 times, go back down through a pulley at the bottom of the tunnel frame and go back up to the drop down frame to be a loop. I was going to have an extension overload spring in the cable to maintain tension. It would have worked but was going to be a lot of parts and pieces and fabrication plus the gearmotor is a surplus item for which I’d probably never find a replacement for in several years when one went bad.
I had also looked at using linear actuators and one in particular that has a control module with keypad that has three programmable buttons to set three positions into it’s memory.
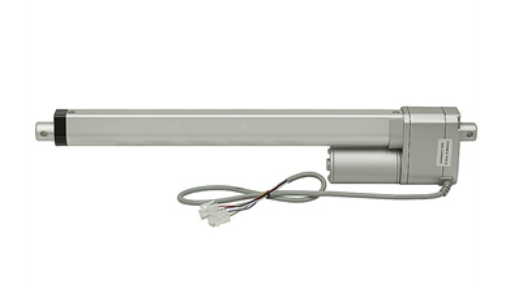

Once programmed, the keypad can be removed from the module and there are three wires, one for each programmed position. Pulse a wire with ground and it goes to that position. The linear actuator is $150 and the module $100 and I was planning on four drop downs, two per side so that would have been $1,000. I went back and looked at them at Surplus Center and also found them on Northern Tool. Northern Tool had a different piece of literature as a pdf than Surplus had. Between three different pdf files, they give you enough info to use your own controller with the built in potentiometer of the actuators to control them. You can set as many stopping points in the travel as you want by using resistance readings to know the position and applying 12vdc to the actuator. I will still need the two SPDT relays to reverse polarity to change directions of the motor for in/out or in my case, open/close. I won’t need limit two switches to stop at open/closed and a proximity sensor to stop in between. The actuator has limit switches built in and a potentiometer to stop at a mid way point.
The first tidbit of info;
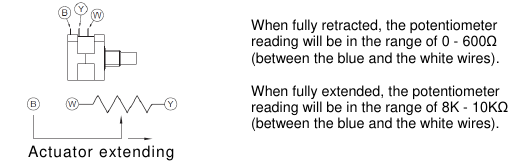
0-600 retracted and 8-10k extended so 4-5k should be about half way. I’m wanting 80% closed as an option, so I can just run it to that point and take an ohm reading. Input that into my controller and use it as a trigger to cut voltage to the actuator when it gets to that reading.
Tidbit two, the wiring schematic and mention of the reference signal(+ 5 VDC excitation).
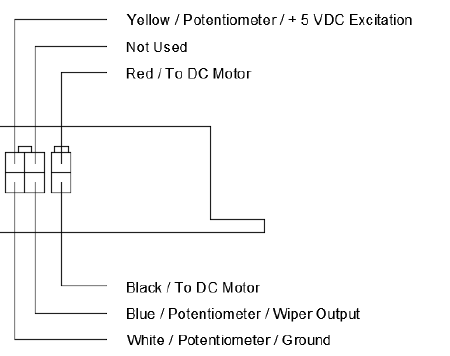
They even have a wiring schematic showing how to reverse polarity/direction using two SPDT relays like I was going to do with the greamotor/cable.
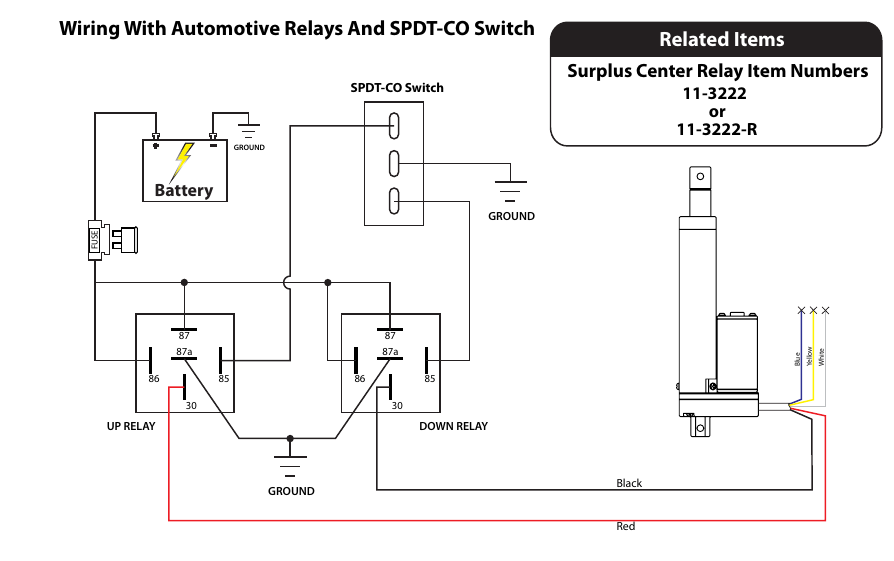
I may go with a single, full length drop down for each side instead of two but in either case, I won’t need to buy their three button programmable controllers for $100 ea. I will however need to buy a $330 analog input module to go with the X-400 Main IO Controller. The X-22s is an 8 analog input module that also has 5 vdc Vref output signal.
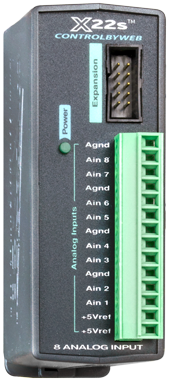
The X-22s will probably some in handy for reading a wind speed/direction sensor and high wind is why I want the ability to close the drop down sides 80% of the way when I’m not here to do it manually. That and a temperature sensor will be used to open/close the sides. That’ll be yet another learning experience in electrical components and their signals. Digital is easy as it’s just on/off or true/false or in computer language, 1/0. Analog is harder and also twice the price when it comes to the components and controllers.
I’ll still be using the some of the SPDT 15 amp relays on the Quad units but they’ll run linear actuators instead of gearmotors.
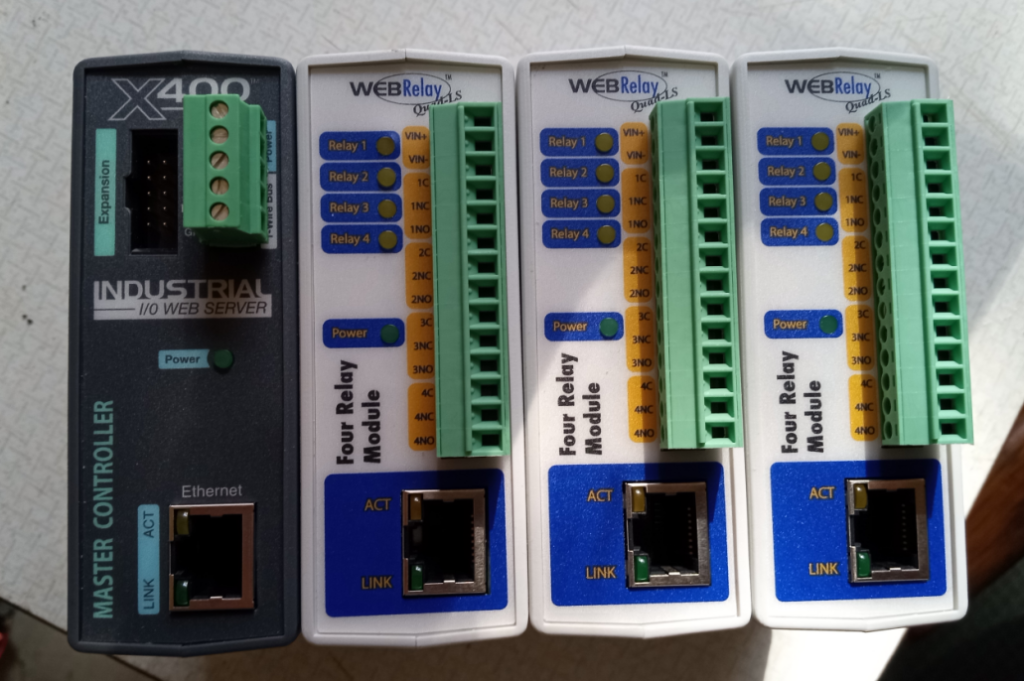
I tested the SPDT relays to run the gearmotor in either direction. No logic or automation because I have no temperature wind speed sensor. Just clicking buttons on the control page from my laptop which I thought was cool. I did set a short time schedule and had it turn one direction for 20 seconds, stop and then in 20 seconds, turn the other direction for 20 seconds.
Not a big fan of the front wiring but I did at least get it neatened up by getting 12″ cat5e cables. Way better than an overly long cable all coiled up which drives me nuts. In some cases, it necessary because the cable end is custom, molded on and not replaceable. The network switch is an industrial unit and has an uplink port that I ran to my internet modem/router which allows me to see the control pages with my web browser at 192.168.1.***
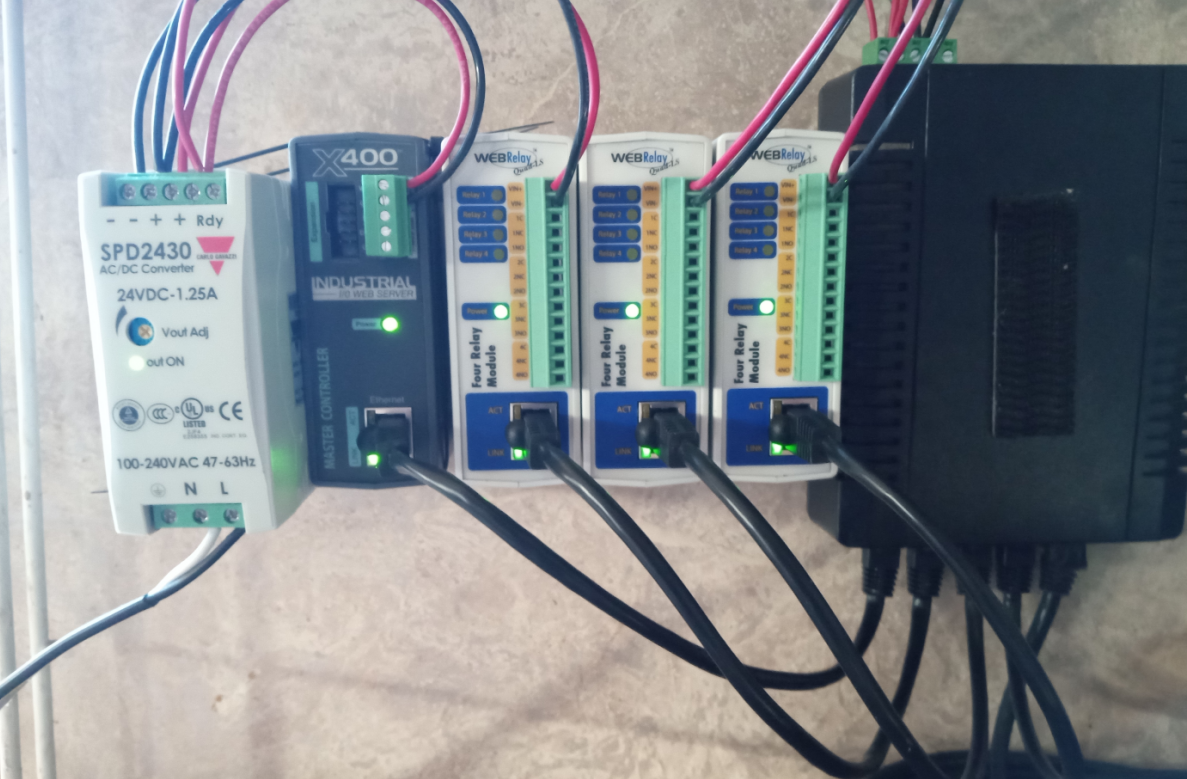
I’m still going to keep the Unitronics V120 as an irrigation controller.
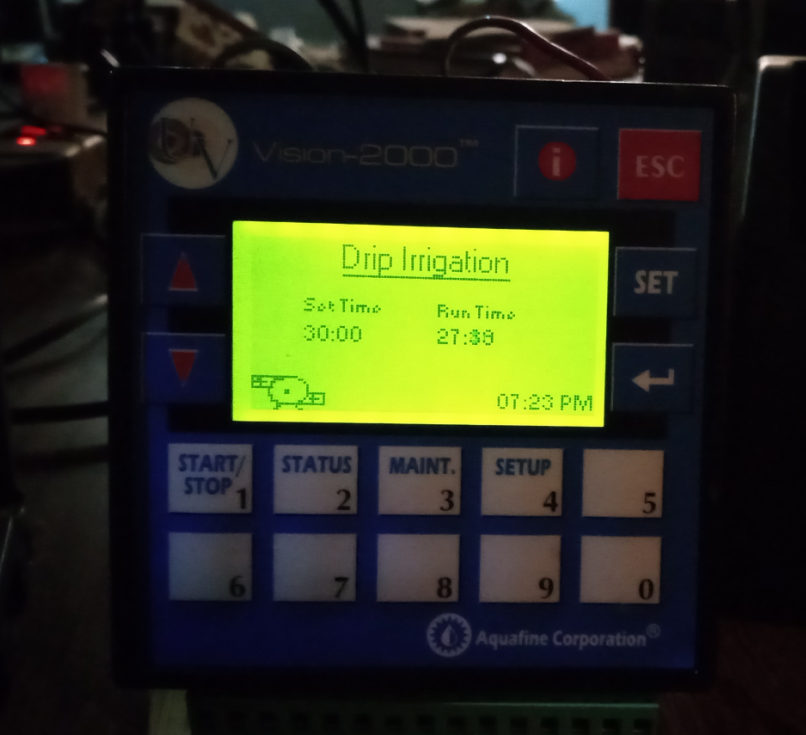
This one’s a branded unit but the one I bought that has the original Unitronics face is bricked. I followed along with a video tutorial for Timers to do the above. When the unit’s powered up, you enter a time duration in minutes and seconds, hit Return and then hit 1 to start which activates one of the relays. Once the time is up, it shuts off the relay and you hit 1 again to run the same time duration. Power has to be cycled to enter a new time but that could be changed. I watered the garden once with this. Hours/minutes is what would be used for drip irrigation but seconds was better to testing. It’s easy to change but I’ve since found an full example for time/date based programming and that will allow me to create multiple schedules and choose one to run. It also has day of the week, month, year etc. I’m sure I can figure out how to be able to add a new schedule via the keypad too.
Someday maybe I’ll replace it with a V130 because most of the V series are butt ugly but these things just look good, to me, probably because I’ve been running Thinkpad laptops for close to 20 years and white lettering on black keys just looks normal.
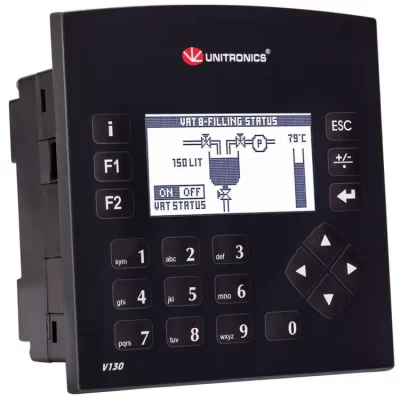
When I bought the V120, I thought it would teach me about electrical stuff but all it taught me was a little about Visilogic, the program for ladder logic for Unitronics PLCs and I have no illusions or even desire of becoming a PLC programmer at my age.
For my own use, I like the Control By Web products for ease of programming. It’s just web pages with buttons, drop down selections and text fields. Tasks can be time/date based or conditional as below.
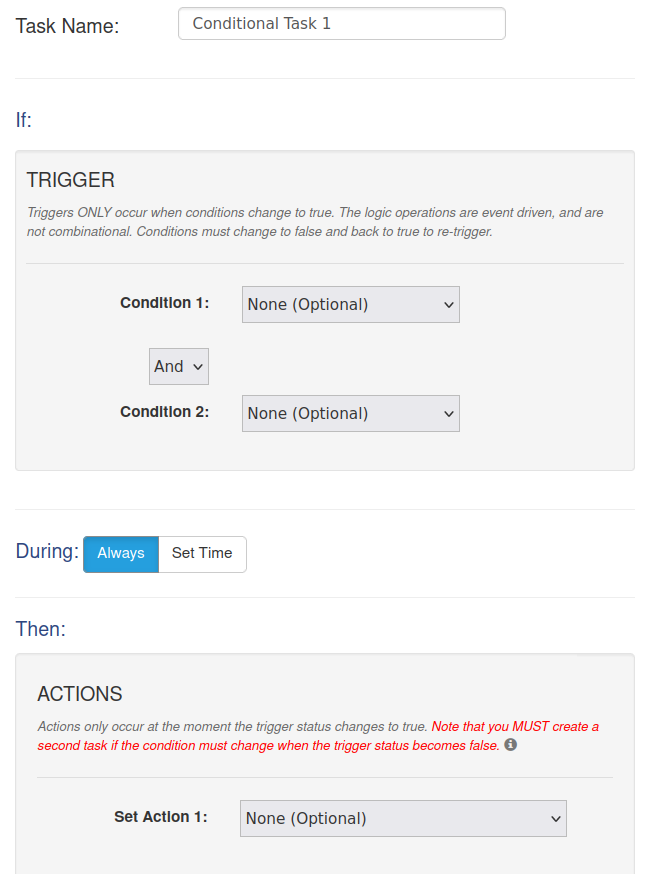
Because Visologics is crazy

In either case, it’s the electrical parts and pieces and signals I need to learn.
The high tunnel is a project I’ve been sitting on since I got curved pipe from an old quonset style hay shed 5-6 years ago. I figured now would be a good time to build it and since I’m not here all the time, and work at a place with a lot of automation, automate it. I had already been thinking of automating it because I know I would have forgotten to open it up one day and my veggie plants would get cooked. Sometimes it will be open or closed both day and night but Spring/Fall, it needs to be opened and closed every day.
It’s costing me a pretty penny but it’s the only way I can learn something about electricity other than it will shock the shit out of you. I can’t just read and memorize stuff like my autistic son with his photographic memory. I have to be able to see how something works. Potentiometers are a decent visual with their coiled up wire inside that the wiper, wipes on, and now I can sort of visualize how a thermocouple works knowing that different metals have different resistance depending on their temperature. A potentiometer as a sensor, who’da thunk it?
It’s always irked me that I didn’t know electrical other than house wiring and basic car stuff but I like tech gadgets and I’ve ever since I got out of school, have loved learning so the controllers are just the thing to drive me to learn electrical. I also like my tools and just grabbed two 7 pc sets of Wiha precision screwdrivers for $40 because all I have is some old worn out things and I don’t want to ruin the screw heads on a $2-300 controller. Now I can give the few Wiha screwdrivers I scavenged from unused tool carts at work to the next guy in line, and have a full set for there and one for home. They’re in Springfield right now so hopefully they’ll get here tomorrow.
I’m too old to learn a new trade and too poor to be spending all this money but I gotta do something to not be relegated to filters and grease guns.